PROCEDURES
In both cleaning and welding services, we emphasize quality, safety, and customization to meet client expectations efficiently. Detailed procedures for each technique, including material selection, processes, common challenges, and solutions, ensure that every service is delivered to the highest standards. Additionally, our consulting and failure analysis services support clients in optimizing their operations and troubleshooting issues effectively.
Customized Cleaning & Maintenance
Description: Maintenance and cleaning needs are customized for each company. We offer daily, weekly, or monthly cleaning contracts or one-time services based on your preferences.
Post-Construction Building Cleaning
Description: For construction companies or new building owners, we provide a thorough cleaning service to prepare for the official opening or move-in.
Welding Services
Laser Welding
Description: A modern technique using light beams to melt and fuse metal parts. Can be applied to aluminum, stainless steel, titanium, and HSLA steel.
How It Works: High power density for controlled heat in the weld area.
Materials: Solid-state, gas, and fiber laser.
GMAW or MIG Welding
Description: Gas metal arc welding using a continuous wire feed for higher deposition rates. Ideal for both aluminum and steel welding.
Advantages:
Can be used in all positions
High deposition rates
Reduced need for cleaning after welding
Semi-automatic process
MIG Welding Shielding Gases
Description: The arc plasma and shielding gases stabilize the weld pool. Common gases include:
Argon
Argon/Helium
Argon with CO2 or Oxygen
Common Welding Issues
Weld Discontinuities: Channel, incomplete fusion, porosity, weld cracks.
Welding Problems: Oxidized weld deposits, wire issues.
WELDING SERVICES
Welding Processes and Techniques
Welding is a manufacturing or sculpting process that joins parts, usually metals or thermoplastics, by creating coalescence. This process often involves melting the workpieces and adding a filler metal to form a weld pool that solidifies into a strong joint. Welding can be accomplished using various energy sources, including gas flame, electric arc, electron beam, friction, and ultrasonic.
TICAM Group Welding Techniques
Laser Welding
MIG Process
TIG Process
Electron Beam Welding (EBW)
EBW is a fusion welding process that applies a high-speed electron beam to produce heat at the weld point. It offers:
Advantages: Single passes for welding thick joints, low distortion, narrow weld zones.
Limitations: High equipment costs, time constraints, and potential for high cure speed causing cracking.
Plasma Arc Welding (PAW)
Similar to the GTAW process but with a higher energy concentration, the PAW process allows for separation of the plasma arc from the shielding gas envelope.
Soft Welding and Brazing
These processes join parts without melting the base metals, suitable for electrical connections and mechanical welds.
Techniques Include: Soft soldering for pipes, stained glass, and mechanical connections; brazing techniques such as silver soldering and gas brazing.
Arc Welding
Produces heat by creating an electric arc between an electrode and the base metal.
Electric Resistance Welding (ERW)
Uses electric current and mechanical pressure to produce heat that forms the weld. Techniques include spot welding and projection welding.Common Concerns and Solutions
We can help you optimize your welding processes by evaluating current parameters and eliminating common weld problems such as:
EBW Process Problems: Channel, porosity, cracking.
Soldering and Brazing Problems: No wetting, excessive wetting, flux occlusion.
Resistance Welding Discontinuities: Cracks, porosity, improper weld penetration.
Equipment Failure Analysis
Our materials engineering and metallurgists provide independent expert opinions in the analysis of failed welds or equipment. Features include:
Weld failure analysis.
Root cause analysis determination.
Photographic documentation.
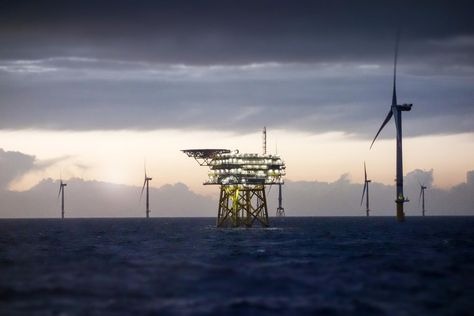
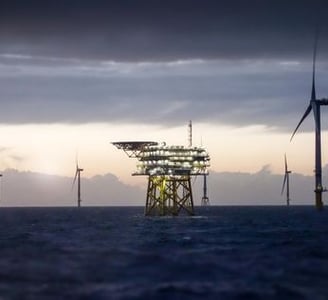
TICAM INTERNATIONAL LIMITED
TICAM International
2231 East Division Street,
Arlington, TX 76011
Phone: 210-41-TICAM, 214-584-8387
Email: info@ticamgroup.com
Website: www.ticamgroup.com
TI-CAM SA Cameroon
Z.I. Wouri Base CEPM
B.P. 1247, Limbé, Cameroon
Phone: (237) 33 47 26 80
Locations
TICAM International Nigeria
Abuja: Suite M210,
251 Herbert Macauley Way,
Central Business District,
Abuja-FCT, Nigeria
Phone: (234) 806 233 5316
Email: info@ticamgroup.com
Port Harcourt: 16A Marina Close, Woji, Port Harcourt, Rivers state, Nigeria.
Phone: (234) 7011263564
Email: info@ticaminternationallimited.com
© 2024. All rights reserved.
Support